The insulation time of the vacuum flask depends on the structure of the flask and the thickness of the materials used.
Generally speaking, the thinner the material of the flask, the longer the insulation time. However, the flask is more prone to damage and deformation, affecting its lifespan; measures such as wrapping the outer layer of the vacuum flask’s inner liner with a metal film and copper plating can also enhance insulation; large capacity and small diameter vacuum flasks have longer insulation times, while small capacity and large diameter vacuum flasks have shorter insulation times; the lifespan of a vacuum flask also depends on the cleanliness of the inner layer and the vacuuming time, with the most important factor being the structure of the vacuum furnace.
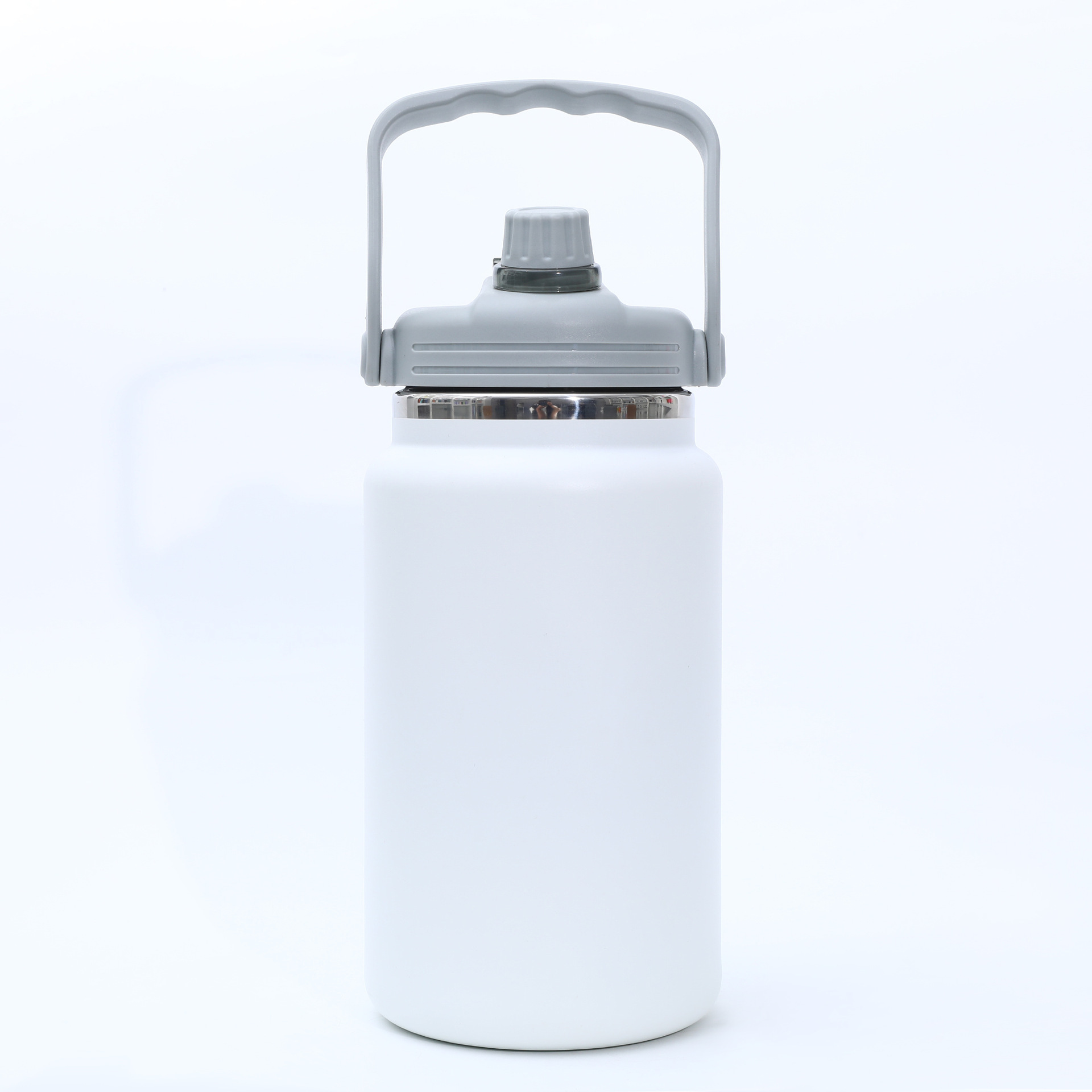
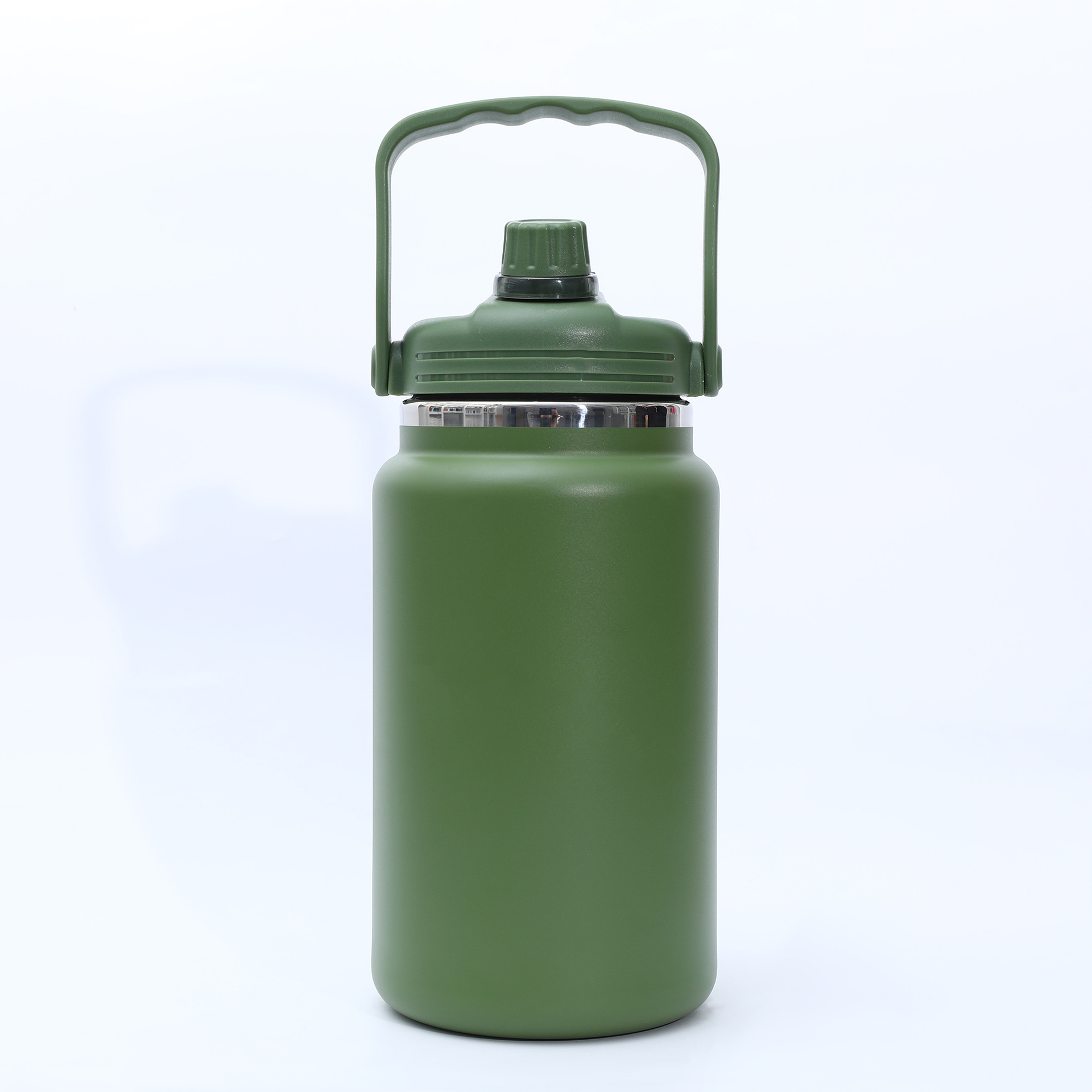
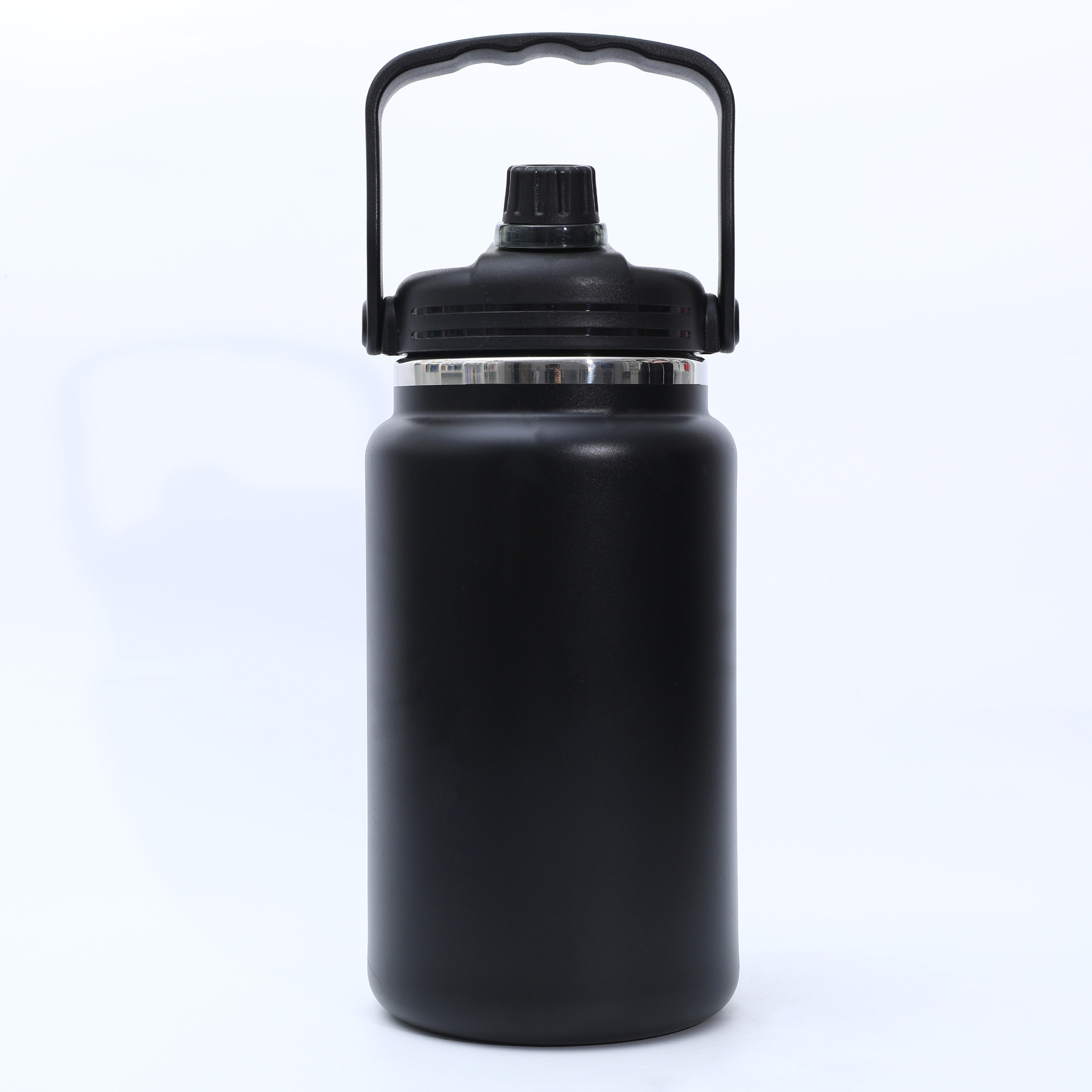
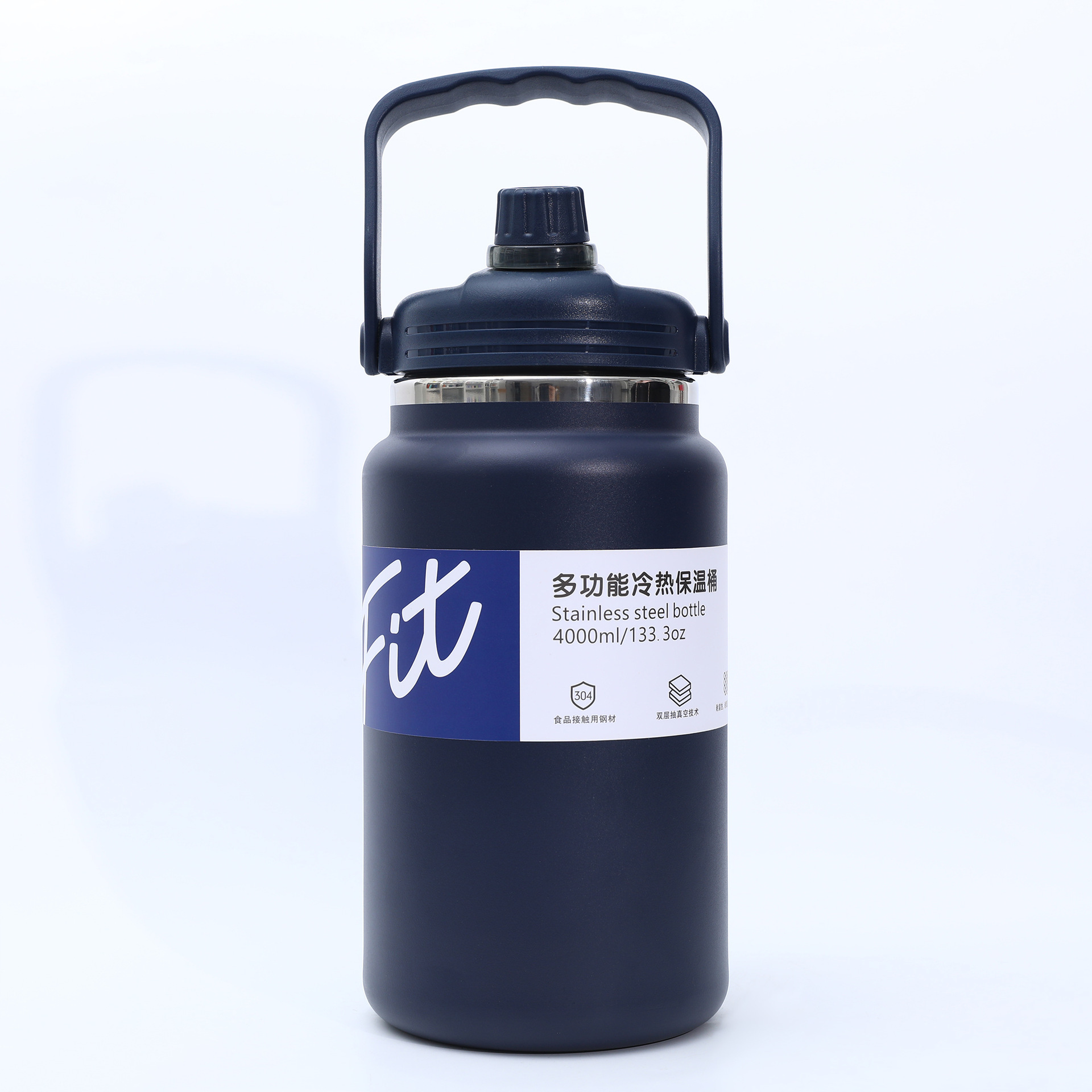
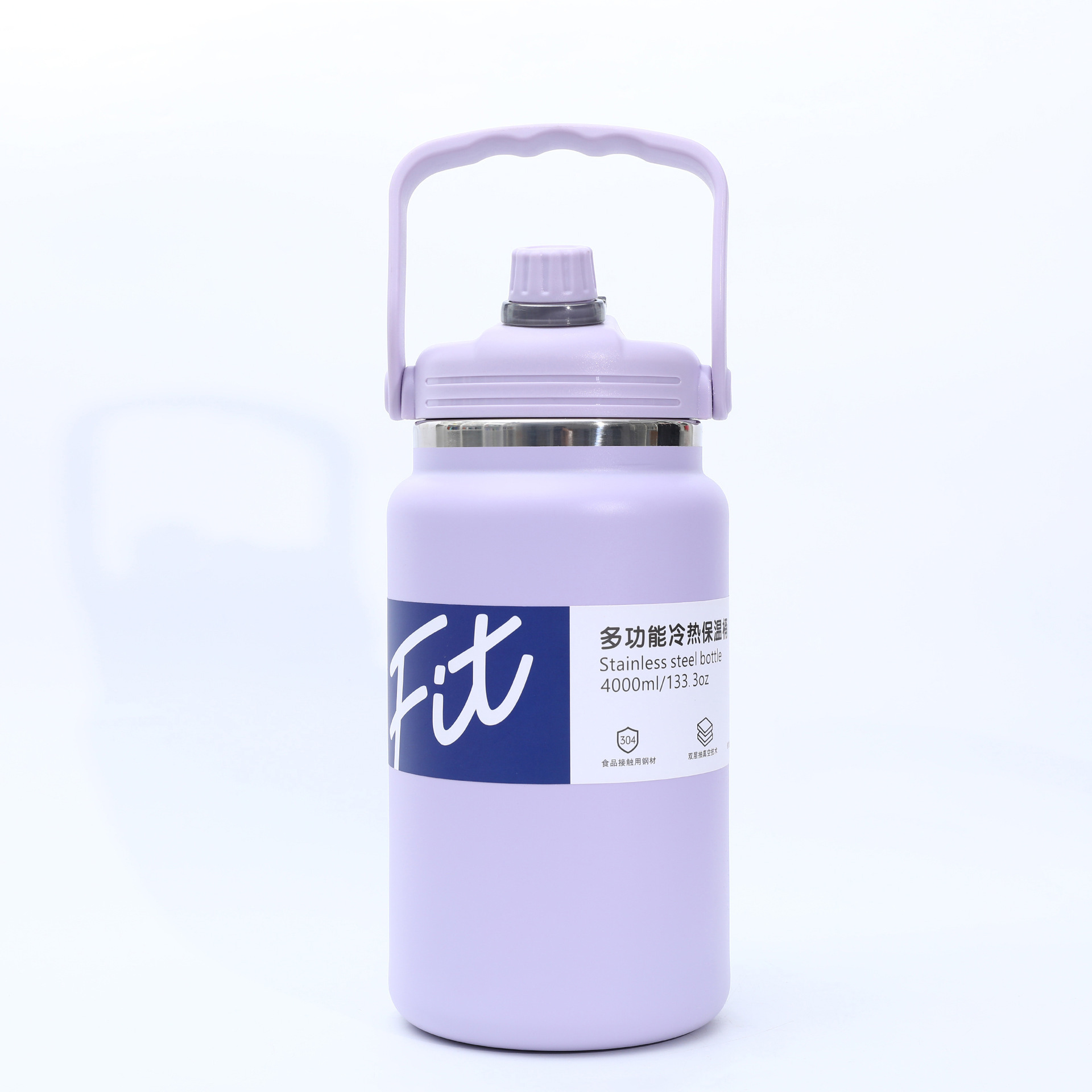
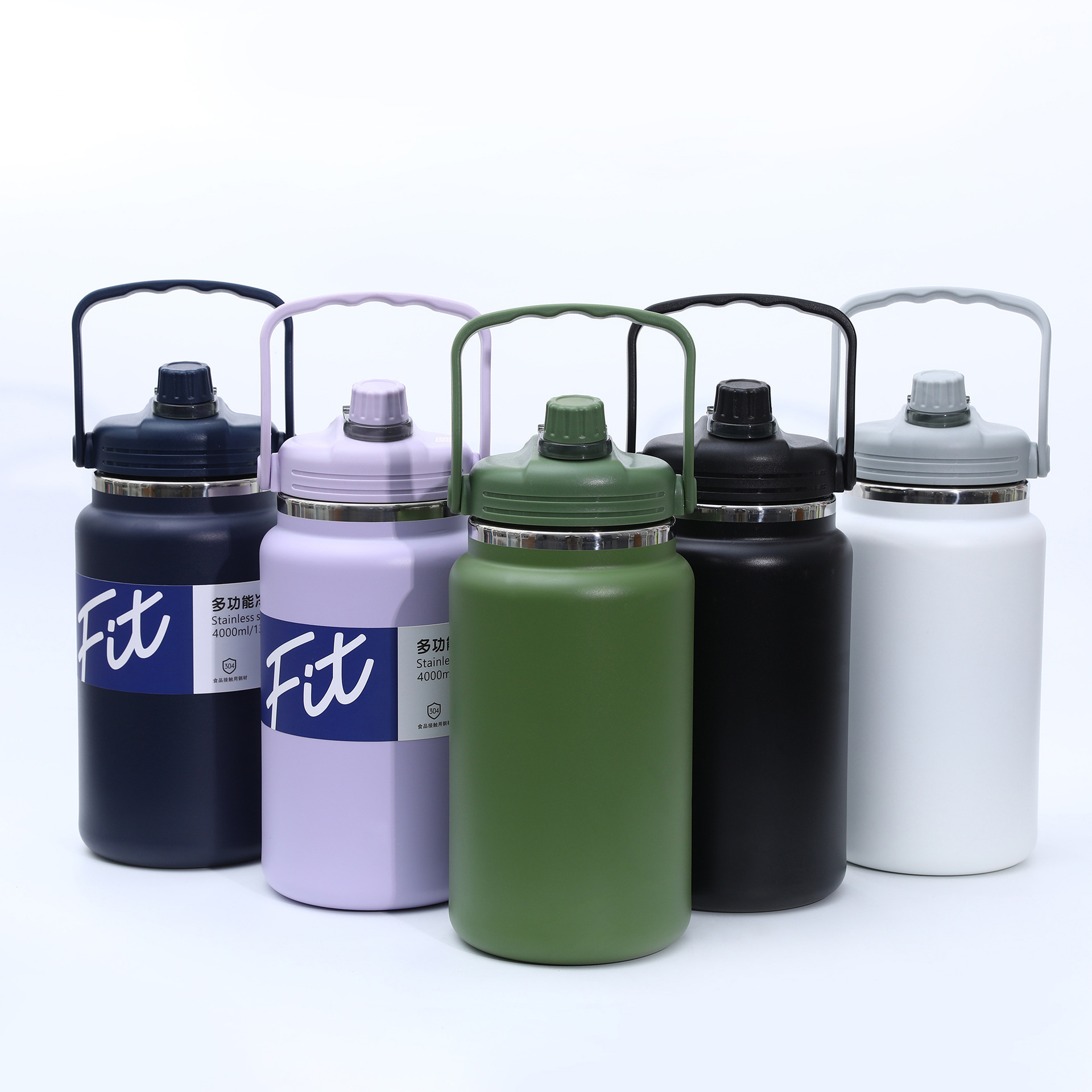
The vacuum equipment used in society for vacuum insulation flasks includes vacuum exhaust tables and vacuum brazing furnaces, which can be roughly categorized into two types with four variations. One type is the tail vacuum exhaust table; the other type is the brazing furnace. The brazing furnace type is further divided into: single chamber, multi-chamber, and high-speed multi-chamber.
Single furnace integrated vacuum brazing furnace. This furnace has a long vacuuming cycle time, and if manufacturers want to improve production efficiency by shortening the vacuuming time, it will affect the lifespan of the flask. The lifespan of the flask is only about 8 years. The tail vacuum flask exhaust table has advantages: the vacuum flasks produced using the tail exhaust vacuum table have a heating temperature of about 500°C during vacuuming, making the outer shell of the vacuum flask less prone to deformation, but the welding points of the copper pipes are easily damaged, requiring special protection during semi-finished product processing.
In addition, there is a major category of vacuum brazing furnaces, which can be roughly divided into three types. Surprisingly, although the vacuum insulation flasks we commonly use look similar to ordinary insulation flasks, the manufacturing process of vacuum insulation flasks is much more complex than that of ordinary insulation flasks, and the technical difficulty is also much higher. Therefore, the price of vacuum insulation flasks is at least twice that of ordinary insulation flasks.